The Advantages Of Micro Tig Welding For Pipe Applications In The Oil And Gas Industry
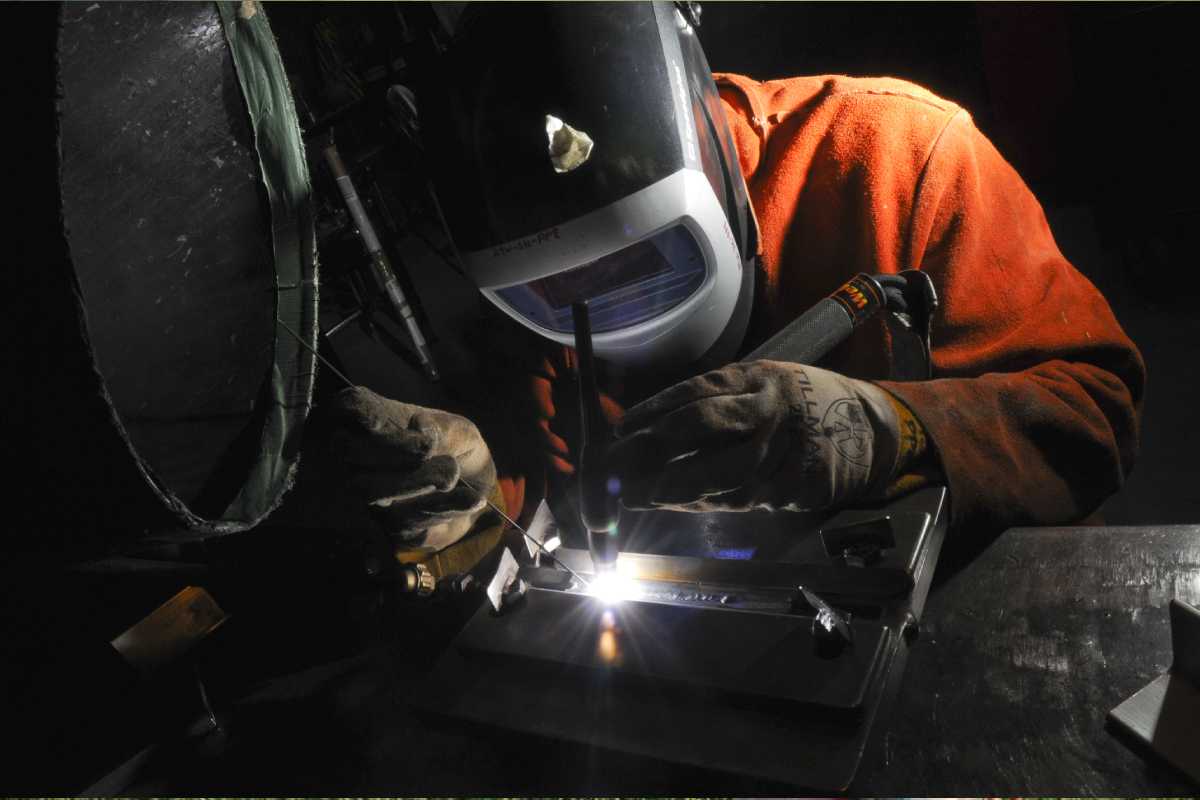
Pipes are essential to the oil and gas industry. They are integral to several systems because they move gases, fluids, and other things. When it comes to pipe applications, the welding process is crucial. It establishes the pipes’ integrity, robustness, and longevity. Micro TIG welding has become the dominant technique for pipe joining in the oil and gas industry thanks to its capacity to produce clean, high-quality welds and exact control. Explore the benefits of utilizing micro TIG in pipe welding situations.
Table of Contents
The Ability to Work with Different Pipe Materials and Thicknesses
The Micro TIG welding method is appropriate for various materials and thicknesses. These comprise carbon steel, aluminum, stainless steel pipe, and rare alloys. This qualifies it for various pipe applications in the oil and gas industries.
Moreover, Micro TIG welding can easily handle pipe walls that are either thin or thick. Welders can match the thickness of the pipes by adjusting parameters like welding speed and heat input, thanks to precision control. Micro TIG welding is suitable for various pipe applications, from thin-walled to thick-walled oil and gas pipelines, because of its adaptability.
Better Control and Precision
Enhanced control and precision are two of Micro TIG welding’s primary benefits for pipe applications. Welders have total control over the welding process because the nature of the welding process guarantees precise and reliable outcomes. This is especially crucial when dealing with pipes that require exact fit and alignment.
Welders can modify the heat input and other settings with micro TIG welding to meet the application’s needs. This degree of control makes it possible to produce accurate, clean welds that satisfy the highest quality requirements. It ensures that the joints are robust and leak-proof, regardless of the pipe’s diameter—small or huge enabling them to endure the application’s requirements.
Minimal Warping and Heat Distortion
Heat distortion and warping are frequent problems when welding, especially in pipe applications. Welding heat can cause the base material to expand and compress. This causes flaws like bending and distortion, which impair structural integrity and cause joints to become misaligned. All of them lead to higher maintenance and repair expenses.
Micro Tig welding reduces heat distortion and warping because it requires less heat input and has perfect control. The tungsten’s concentrated heat source enables localized heating, which lowers the heat-affected zone, minimizing bending and distortion to keep the pipes properly aligned and shaped.
Excellent Weld Quality and Visual Appeal
Last but not least, micro TIG welding is well known for creating strong and aesthetically pleasing welds. The combination of a shielding gas and tungsten electrode, together with careful control, produces neat and attractive welds. This is crucial for pipe applications where the welds’ appearance can play a significant role. MicroTIG welds from Micro Weld, Inc. are more aesthetically pleasing, substantial, and durable.
The base metals can fuse completely thanks to this process. This results in a strong connection that can endure pressures and strains in pipe applications. It guarantees the integrity of the welded joints while simultaneously ensuring the pipes’ long-term functionality and stopping leakage. The Advantages Of Micro Tig Welding For Pipe Applications In The Oil And Gas Industry