A Complete Guide to Arc Flash Labeling: What You Need to Know
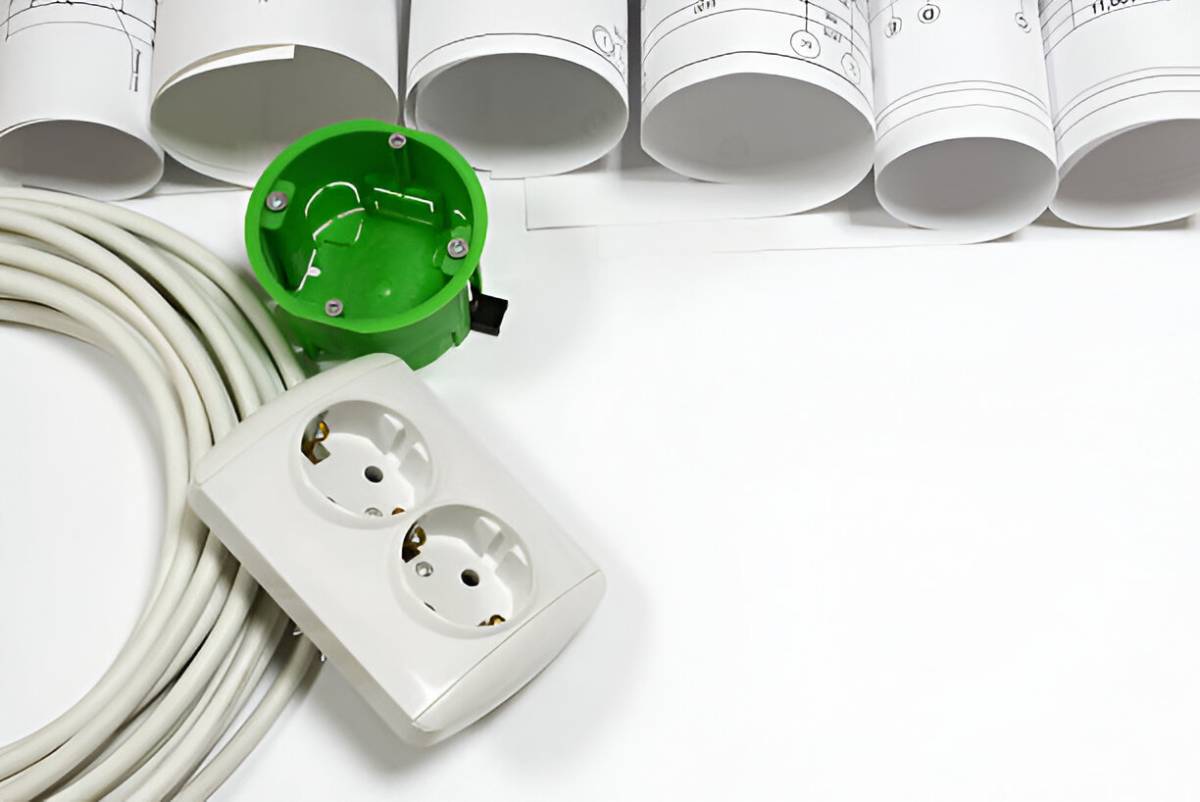
Arc flash labeling are a necessary precaution for any location that involves electrical systems. These labels are aimed at reminding personnel about the risks of arc flash, which can lead to severe injuries or death if the necessary precautionary measures are not taken.
Beyond serving as a caution, arc flash labels serve a powerful purpose within protection procedures and standards legislation. These labels elevate workers’ knowledge, enabling them to use and maintain electrical equipment without many hazards that can be fatal, hence increasing efficiency.
Here you’ll find a brief overview of what arc flash labeling is, why it is required, and how it must be done.
Table of Contents
What Is Arc Flash Labeling?
Arc flash labeling entails placing specific markers or labels on equipment dealing with electrical power to help personnel understand the risks of arc flash. An arc flash happens when an electrical shock occurs that produces a dangerous amount of light, heat, and pressure. This helps guard workers against risks before engaging with or maintaining any piece of equipment.
Why Is Arc Flash Labeling Necessary?
a. Ensures Worker Safety
Arc flash incidents often result in severe burns, impaired or complete vision loss, and fatal consequences. Labeling decreases the risks by explaining the degree of hazards and what kind of PPE is necessary to perform the tasks safely.
b. Facilitates Maintenance
Appropriate and consistent labeling makes repairs faster and easier to complete, with a lower risk to technicians working on the electrical systems.
What Is Contained on an Arc Flash Label?
Arc flash labels must include critical information to ensure clarity and compliance:
a. Warning Signal
Labels have to display a graphic that would be easily identifiable as a warning of danger.
b. Arc Flash Boundary
This will tell you the safe approach distance to the equipment—from which one is protected from an arc flash.
c. Incident Energy Level
A measure of the energy let off during an arc flash, most commonly presented in calories per square centimeter (cal/cm²).
d. Required PPE
The label outlines the protective clothing required while operating in the vicinity of the equipment.
e. Equipment Details
Information related to that particular piece of equipment, such as voltage or identification number.
Conduct a Hazard Analysis
A risk matrix, based on the arc flash hazard analysis, identifies the risk levels of all the electrical equipment. This process determines where a label is needed and what message the label must convey.
a. Use Durable Materials
Labels must be made to endure different conditions such as heat, cold, humidity, and chemicals. Materials like abrasion-resistant fabric, textile polyester, or laminated vinyl would be sufficient.
b. Regularly Update Labels
Electrical systems may change over time due to alterations or enhancements. It is important to change labels if there is a change; sometimes it is because the label is no longer safe for use.
c. Train Employees
Training ensures that the workers are aware of how to approach arc flash labels. This also emphasizes the centrality of compliance with the recommended guidelines—for safe working practices.
Conclusion
Arc flash labeling is an essential factor to consider in electrical risk control. As a sign of danger and information, these labels safeguard employees, enforce rules, and support effective care. The issues of labeling and relevant regulations should be followed—it will help ensure appropriate working conditions within your organization.
Also Read: How Blockchain Technology Is Transforming Global Shipping and Logistics