The Vital Role Of Precision Measurement In The Oil And Gas Industries
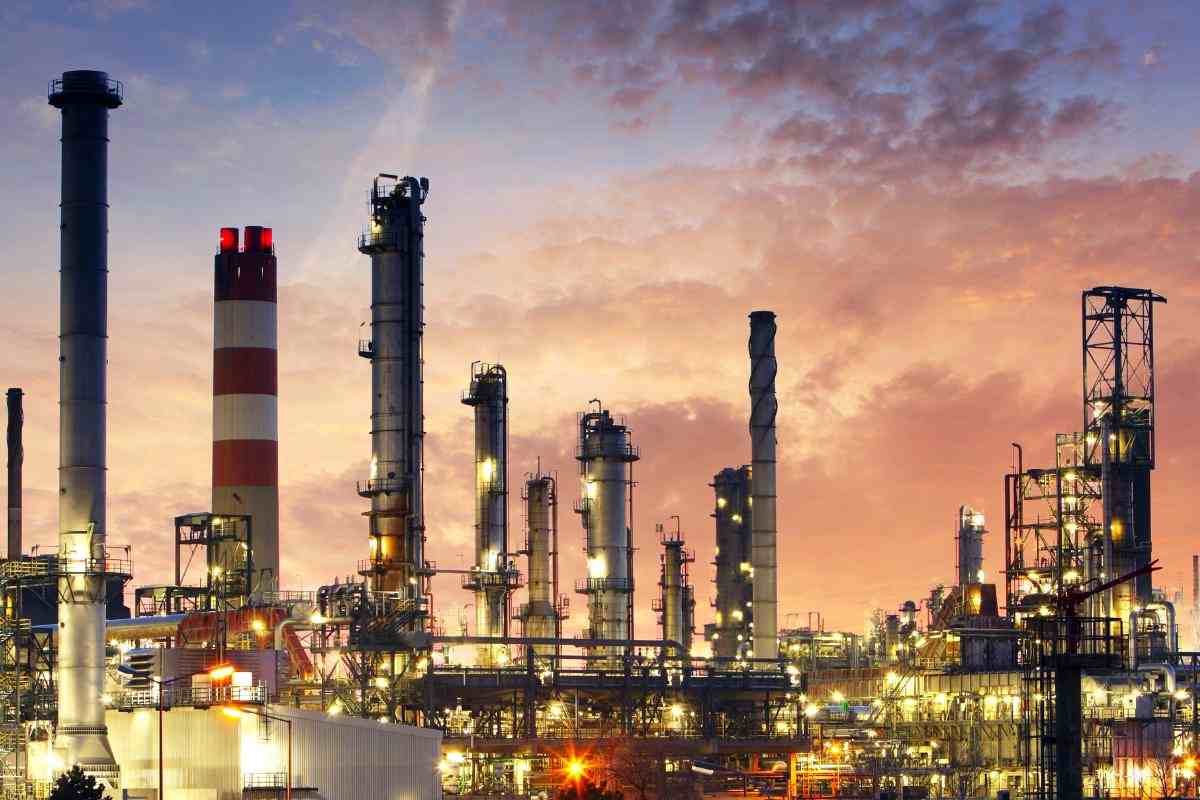
In the bustling world of the oil and gas industry, the significance of precision measurement might seem negligible at first glance. Yet, its pivotal role in ensuring safety, optimising efficiency, and maximising profits makes it an unseen hero in this complex sector. This article delves into the world of precision measurement, highlighting its importance, the potential risks of neglecting it, and strategies for proper maintenance to ensure long-term reliability.
Table of Contents
Understanding Precision Measurement
Precision measurement is a term that encapsulates the methods and tools used to obtain precise measurements of various quantities. From the oil and gas sector to the medical and pharmaceutical industries, these measurements are critical for the smooth operation of countless processes.
What is Precision Measurement?
In the broadest sense, precision measurement involves the use of specialised tools and procedures to gauge physical quantities with a high degree of accuracy. This includes, but is not limited to, instruments like dial gauges, micrometres, and callipers. Precision measurement is pivotal in sectors such as medical and pharmaceutical, manufacturing, automotive, and, of course, the oil and gas industry.
Why is Precision Measurement Important?
The importance of precision measurement in the oil and gas industry is multi-faceted. It is a cornerstone of safety, ensuring that equipment functions properly and mitigating the risk of accidents. It also bolsters efficiency, enabling firms to optimise processes and maximise output. Additionally, precision measurement is a key determinant of product quality, directly influencing the reputation and profitability of oil and gas companies.
The Role of Precision Measurement in the Oil and Gas Industry
The oil and gas industry is a realm of extreme conditions and high stakes. Here, precision measurement takes on a heightened importance, playing a crucial role in everything from extraction and processing to distribution.
Ensuring Accurate Measurements
In the oil and gas industry, precise measurements are fundamental to the accurate evaluation of extracted resources. The sector often relies on advanced weighing systems, such as industrial weight scales, to ascertain the exact quantity of oil and gas extracted from the ground. This ensures that firms receive the correct compensation for their products and maintains the integrity of the supply chain by verifying that customers receive the exact quantity of oil and gas they have purchased.
Improving Efficiency and Productivity
Precision measurement also plays a vital role in enhancing efficiency and productivity in the oil and gas industry. Accurate measurements enable companies to optimise their production processes, facilitating the precise control of variables such as temperature, pressure, and flow rate. This, in turn, allows companies to maximise their output and, by extension, their profits.
Safeguarding Worker Safety
Worker safety is a paramount concern in the oil and gas industry, given the hazardous environments in which it operates. Precision measurement contributes significantly to safety by ensuring that equipment operates within safe parameters. For example, the precision calibration of flare gas meters is vital to prevent the build-up of pressure and the risk of explosion.
The Repercussions of Neglecting Precision Measurement
Neglecting precision measurement can have severe repercussions for oil and gas companies, ranging from financial losses to safety hazards and operational disruptions.
Financial Implications
Inaccurate measurements can lead to significant financial losses at various stages of the oil and gas value chain, from exploration and production to distribution. Companies risk producing or distributing sub-optimal quantities of oil and gas, which can result in unrealised profits or even financial penalties.
Safety Concerns
The safety implications of neglecting precision measurement are particularly grave. Equipment that is not regularly calibrated can yield incorrect measurements, potentially endangering the workers who rely on this data. In the worst-case scenario, this could lead to catastrophic accidents, such as explosions in processing plants.
Operational Disruptions
Failing to maintain and calibrate equipment can also lead to operational disruptions, such as unplanned plant shutdowns. These can be incredibly costly, both in terms of lost production and the expense of repairing or replacing faulty equipment. For instance, companies can lose millions of dollars due to unscheduled shutdowns caused by equipment failure.
The Importance of Regular Calibration
Calibration is a critical aspect of precision measurement, ensuring that instruments and equipment continue to provide accurate readings over time. This involves comparing the measurements from the device under test (DUT) with a set of universally accepted reference standards.
The Calibration Process
In the calibration process, a series of sample measurements are taken from the DUT and compared against reference standards. Regular calibration ensures that oil and gas operators can maintain the highest degree of measurement accuracy, reducing uncertainties and aiding in the maximisation of profits.
The Frequency of Calibration
The frequency of calibration is a crucial consideration in precision measurement. To maintain accuracy, equipment must be calibrated regularly. Infrequent calibrations can lead to inaccurate measurements and, in turn, miscalculations that can have disastrous consequences, such as equipment failure and total plant shutdown.
Common Pitfalls in Precision Measurement
Certain common pitfalls can compromise the accuracy of precision measurement in the oil and gas industry. Awareness of these pitfalls can help companies avoid errors and ensure the reliability of their measurements.
Measuring pH Values at Different Temperatures
One common pitfall involves the measurement of pH values at varying temperatures. Precision measurement is crucial in this context, as pH values can deviate significantly from laboratory measurement results. Instruments that are not calibrated may fail to detect these deviations, leading to inaccurate results.
Neglecting the Calibration of Pressure and Temperature Equipment
Another common mistake is neglecting the calibration of pressure and temperature measurement equipment. Some companies focus solely on calibrating their flowmeters, but this can lead to distorted results, as pressure and temperature can significantly affect flow measurement values.
The Role of Technology in Precision Measurement
Technology is increasingly important in precision measurement, enabling companies to monitor and control their operations more effectively. Internet and related applications facilitate a greater flow of information, allowing companies to monitor pump operations, analyse seismic data, and track employees from almost anywhere.
The Use of Technology in Monitoring
With the advent of technology, monitoring operations in remote locations from company headquarters is now possible. This significantly impacts the oil and gas industry, where operations are often located in inaccessible areas.
The Role of Technology in Data Analysis
Technology also plays a crucial role in data analysis. By collating and analysing data from various sources, companies can gain valuable insights into their operations, enabling them to optimise processes and maximise productivity.
The Maintenance of Precision Measurement Instruments
Maintaining precision measurement instruments is crucial to ensuring their long-term reliability. This involves regular calibration, proper storage, appropriate handling, and regular cleaning.
Regular Calibration
Regular calibration is a critical aspect of maintaining precision measurement instruments. This involves comparing the measurements from the instrument with a set of universally accepted reference standards, ensuring that the instrument continues to provide accurate readings.
Proper Storage
Storage is another important factor in maintaining precision measurement instruments. Instruments should be stored in a controlled environment, free from extreme temperatures, humidity, and vibrations. They should also be protected from physical damage and kept in a place where they won’t rub against each other, as this could affect their calibration.
Appropriate Handling
Appropriate handling is also crucial in maintaining precision measurement instruments. Instruments should be handled gently to avoid damage that could affect their calibration. Furthermore, they should be used within their intended range of operation to ensure accurate readings.
Regular Cleaning
Regular cleaning is another critical aspect of maintaining precision measurement instruments. Instruments should be cleaned according to the manufacturer’s instructions, using appropriate cleaning agents to avoid damaging the instrument’s components.
Strategies for Enhancing Precision Measurement in the Oil and Gas Industry
There are several strategies that oil and gas companies can employ to enhance precision measurement and ensure the long-term reliability of their instruments.
Investing in Quality Instruments
Investing in quality instruments from reputable manufacturers such as Eley Metrology is essential. High-quality instruments are more likely to provide accurate measurements and are generally more durable and reliable than lower-quality alternatives.
Training and Education
Training and education are also crucial in enhancing precision measurement. By ensuring that employees are well-trained in using and maintaining precision measurement instruments, companies can minimise errors and enhance the reliability of their measurements.
Conclusion
Precision measurement plays a critical role in the oil and gas industry, underpinning safety, efficiency, and profitability. By understanding the importance of precision measurement, being aware of the potential risks of neglecting it, and implementing strategies for proper maintenance, companies can ensure the long-term reliability of their instruments and safeguard their operations.